Why plastic extrusion is the best choice for mass production
Why plastic extrusion is the best choice for mass production
Blog Article
Comprehending the Essentials and Applications of Plastic Extrusion in Modern Production
In the world of modern production, the strategy of plastic extrusion plays a crucial function - plastic extrusion. This elaborate procedure, involving the melting and shaping of plastic via specialized passes away, is leveraged across various industries for the creation of varied products. From vehicle components to durable goods product packaging, the applications are large, and the possibility for sustainability is similarly remarkable. Deciphering the basics of this procedure discloses real adaptability and potential of plastic extrusion.
The Basics of Plastic Extrusion Process
While it may appear complicated, the basics of the plastic extrusion process are based upon reasonably uncomplicated principles. It is a manufacturing procedure in which plastic is thawed and afterwards formed into a constant profile through a die. The raw plastic material, commonly in the type of pellets, is fed into an extruder. Inside the extruder, the plastic is subjected to heat and stress, creating it to melt. The liquified plastic is after that forced through a designed opening, called a die, to form a long, continual product. The extruded item is cooled down and after that cut to the desired size. The plastic extrusion procedure is extensively utilized in various industries due to its efficiency, adaptability, and cost-effectiveness.
Different Sorts Of Plastic Extrusion Techniques
Structure upon the basic understanding of the plastic extrusion process, it is needed to check out the different techniques involved in this production approach. In contrast, sheet extrusion develops big, level sheets of plastic, which are commonly more processed into items such as food product packaging, shower drapes, and car components. Recognizing these techniques is key to making use of plastic extrusion properly in contemporary manufacturing.
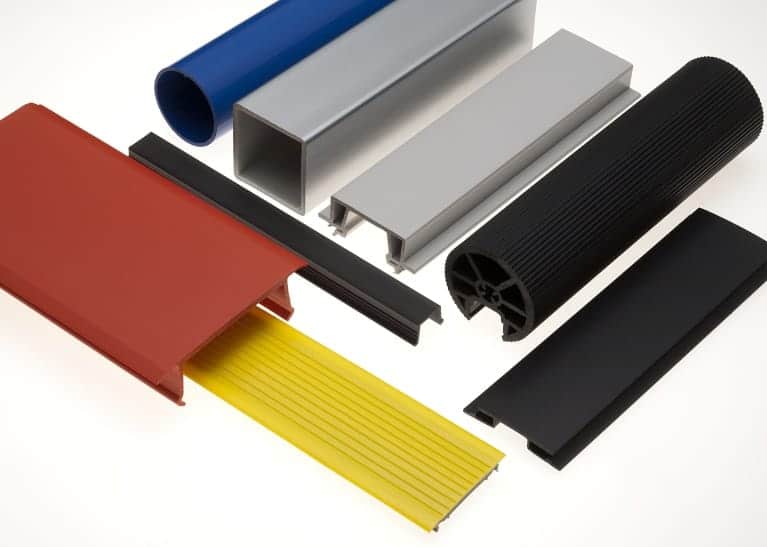
The Duty of Plastic Extrusion in the Automotive Market
An overwhelming bulk of components in modern lorries are items of the plastic extrusion procedure. This process has actually revolutionized the auto market, changing it into an extra efficient, cost-efficient, and flexible production market. Plastic extrusion is mainly utilized in the production of different automobile elements such as bumpers, grills, door panels, and control panel trim. The process gives an attire, constant output, making it possible for makers to generate high-volume components with wonderful accuracy and marginal waste. The lightness of the extruded plastic parts adds to the overall reduction in vehicle weight, enhancing gas effectiveness. The resilience and resistance of these components to heat, chilly, and influence enhance the longevity of vehicles. Therefore, plastic extrusion plays a crucial role in automotive manufacturing.

Applications of Plastic Extrusion in Consumer Product Manufacturing
Past its substantial effect on the automobile market, plastic extrusion shows equally effective in the realm of durable goods making. This procedure is critical in creating a broad array of products, from food product packaging to family home appliances, toys, and even clinical tools. The adaptability of plastic extrusion enables makers to develop and produce complex sizes and shapes with high precision and efficiency. Furthermore, due to the recyclability of several plastics, squeezed out elements can be recycled, minimizing waste and expense. The flexibility, flexibility, and cost-effectiveness of plastic extrusion make it a recommended choice for several consumer goods suppliers, contributing considerably to the industry's growth and innovation. The ecological implications of this see prevalent use call for careful consideration, a subject to be talked about better in the subsequent area.
Environmental Effect and Sustainability in Plastic Extrusion
The prevalent use plastic extrusion in making welcomes scrutiny of its environmental ramifications. As a process that regularly makes use of non-biodegradable products, the ecological impact can be significant. Energy usage, waste production, and carbon discharges are all worries. Industry advancements are enhancing sustainability. Effective machinery decreases energy use, while waste management systems recycle scrap plastic, lowering basic material needs. Furthermore, the growth of biodegradable plastics offers an extra environmentally pleasant option. Regardless of these enhancements, additionally innovation is needed to alleviate the environmental footprint of plastic extrusion. As society leans in the direction of sustainability, producers have to adjust to stay sensible, emphasizing the value of continuous study and innovation in this area.
Conclusion
To conclude, plastic extrusion plays an essential role in modern manufacturing, especially in the vehicle and durable goods markets. Its flexibility enables the manufacturing of a large range of parts with high accuracy. Its potential for recycling and growth of eco-friendly products offers an appealing avenue in the direction of sustainable methods, thus addressing environmental concerns. Comprehending the essentials of this process is crucial to optimizing its applications and advantages.
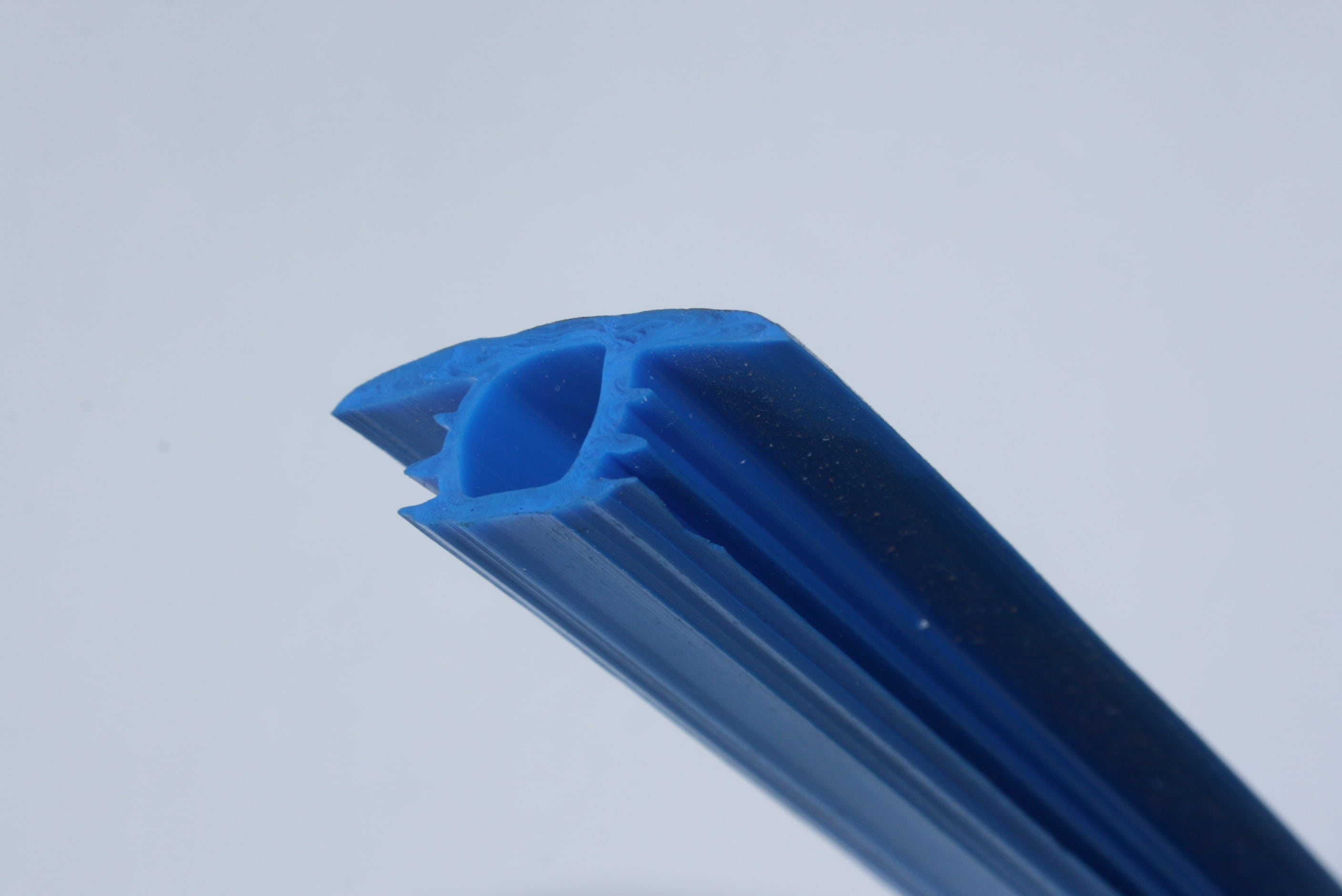
The plastic extrusion procedure is extensively made click site use of in numerous markets due to its effectiveness, cost-effectiveness, and adaptability.
Building upon the standard understanding of the plastic extrusion process, it is necessary to check out the different strategies entailed in this production approach. plastic extrusion. In comparison, sheet extrusion develops big, flat sheets of plastic, index which are typically further processed right into products such as food product packaging, shower drapes, and automobile parts.A frustrating majority of components in contemporary lorries are products of the plastic extrusion process
Report this page